Industrial and medical-grade nitrous oxide differ primarily in their regulatory standards and purity requirements. You’ll find medical N₂O under strict FDA oversight with 99.99% purity requirements, extensive batch testing, and rigorous documentation protocols. Industrial variants follow more relaxed OSHA guidelines with less stringent purity thresholds and quality controls. The distinctions extend beyond basic specifications into specialized storage, handling procedures, and manufacturing processes that guarantee end-use safety and effectiveness.
Regulatory Standards and Compliance
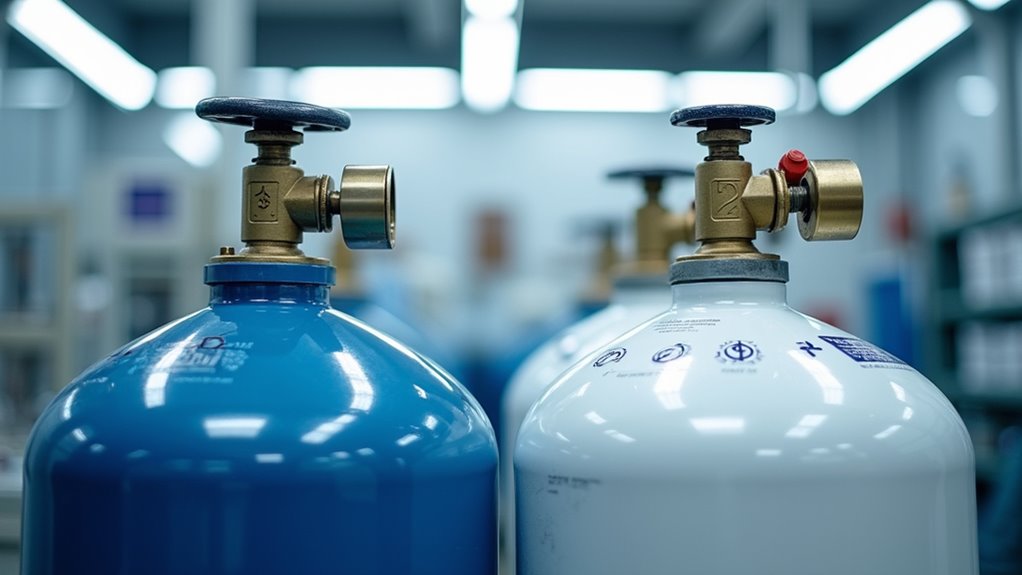
While both industrial and medical grade nitrous oxide must adhere to regulatory standards, their compliance requirements vary considerably in scope and stringency. Medical grade falls under strict FDA oversight through 21 CFR 211 and USP monographs, requiring specific certifications under the FD&C Act. You’ll find industrial grade follows less rigorous OSHA guidelines and ISO 9001 quality management standards.
The recordkeeping requirements reflect this disparity. Medical facilities must maintain thorough batch records, traceability reports, and detailed production documentation, subject to regular FDA audits. Since designated medical gases received streamlined certification under FDASIA in 2012, industrial applications focus primarily on process control documentation with ISO 9001 oversight and auditing. Regular food safety audits and inspections are essential for maintaining compliance with certification requirements.
You’ll need to guarantee medical grade meets USP-defined purity levels for human use, while industrial grade follows broader technical specifications for manufacturing processes.
Manufacturing Process Requirements
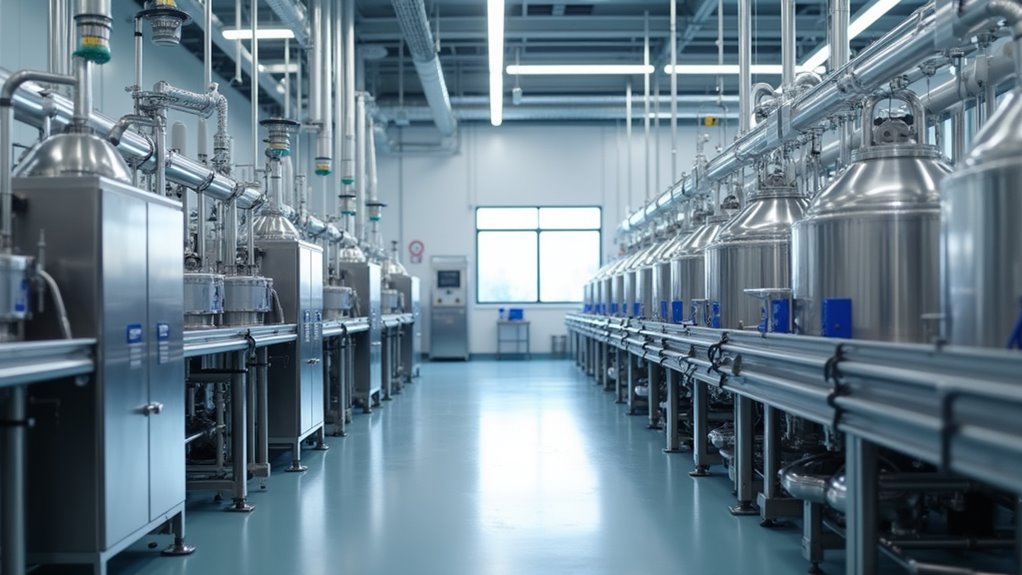
The manufacturing processes for industrial and medical grade nitrous oxide diverge markedly in their technical requirements and controls. You’ll find that industrial production employs thermal decomposition of ammonium nitrate at 275-280°C, requiring specialized equipment integrity and skilled personnel to manage explosion risks. The process demands multi-section melters with precise temperature controls and non-contact heating elements. This industrial process generates a potent greenhouse gas that persists in the atmosphere for over a century.
Critical safety measures include closed-loop recirculation systems and independent temperature monitoring across melter sections. You’ll need to maintain temperatures below 140°C during non-production phases and implement emergency shutdown protocols. The system requires corrosion-resistant materials throughout, while stack gas treatment systems must capture residual N2O and NOx emissions.
Proper handling of technical-grade ammonium nitrate feedstock and careful management of exothermic reactions guarantee consistent product quality.
Purity Specifications and Testing
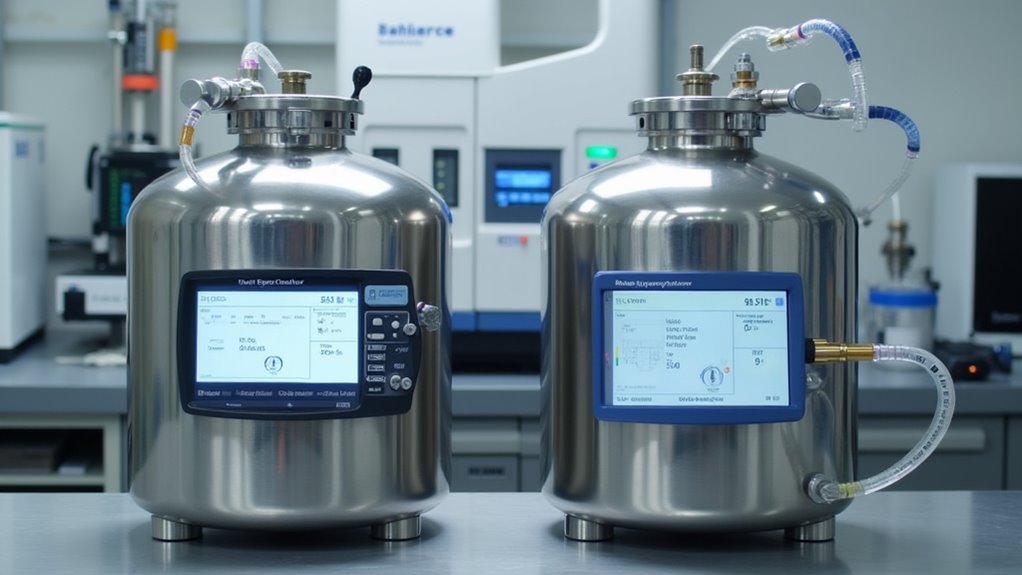
Quality control standards for medical and industrial nitrous oxide reflect significant differences in their testing rigor and purity requirements.
You’ll find medical N₂O requires stringent gas chromatography and spectroscopy testing for each batch, with mandatory Certificates of Analysis documenting levels of critical contaminants like O₂, N₂, and CO₂. Specifically, medical-grade nitrous oxide follows FDA Good Manufacturing Practices to ensure consistent pharmaceutical quality.
Similar to how zero grade nitrogen falls within lower purity ranges between 90-99.9%, industrial grade testing follows standardized quality control protocols but allows higher contaminant thresholds, with less frequent batch testing and simpler documentation requirements. The highest industrial grade nitrous oxide can achieve 99.999% purity under optimal manufacturing conditions.
Quality Control Standards
Maintaining stringent control over gas purity represents a fundamental distinction between medical and industrial grade nitrous oxide specifications. Medical-grade N2O must achieve a minimum purity of 99.99% to meet USP standards, with strict procurement protocols governing raw material selection and processing. Industrial applications typically operate under less rigorous purity requirements. Similar to how liquid helium requires 99.999% purity levels for sensitive applications, medical nitrous oxide demands exceptional quality standards. Medical facilities administer the gas through breathing apparatus for safe delivery during procedures. The gas undergoes multiple distillations during production to achieve the highest possible purity levels.
Quality control measures for medical-grade N2O include thorough testing for sterility, endotoxins, and specific contaminants, with dedicated distribution channels to preserve product integrity. You’ll find that while industrial grade undergoes basic safety testing, it isn’t subject to the same extensive validation procedures.
The medical variant faces stricter regulatory oversight, requiring documentation of each production batch’s composition and impurity levels. These amplified quality controls guarantee consistent performance in clinical settings where patient safety is paramount.
Testing Methods and Frequency
Rigorous testing protocols differentiate medical and industrial grade nitrous oxide across multiple analytical dimensions. Medical grade requires sophisticated analytical techniques like gas chromatography for precise impurity detection, while industrial grade relies on simpler colorimetric tests. You’ll find medical certification processes demand third-party lab verification, whereas industrial testing may be conducted in-house if performed at all.
The testing frequency also varies considerably between grades. Medical nitrous oxide undergoes mandatory batch testing during filling, regular purity checks during storage, and pre-delivery analysis. In contrast, industrial grade testing follows a more relaxed schedule with optional pre-shipment testing and minimal storage monitoring. While medical grade must adhere to strict USP/Pharma standards, industrial grade typically follows basic ASTM or industry-specific guidelines for quality assurance.
Storage and Transportation Methods
The distinct storage and transportation methods for medical-grade and industrial-grade nitrous oxide reflect their divergent end-use requirements. Medical-grade facilities maintain strict cylinder size limits and focused storage capacity planning in temperature-controlled environments between 15-25°C. You’ll find these cylinders secured in fixed racks with brackets, while industrial storage often accommodates larger quantities in palletized configurations. The gas must be stored in an upright position to maintain its stability and prevent potential hazards. All cylinders require adequate ventilation when being stored or used to ensure safety. Following local regulatory guidelines is essential to maintain compliance during storage and transport operations.
For transport, medical-grade nitrous oxide requires insulated carts and specialized carriers to preserve product integrity, with clear “For Medical Use Only” labeling. Industrial-grade cylinders can be moved via open-bed trucks with proper tie-downs.
Both grades need secure storage areas with external ventilation, but medical facilities emphasize contamination prevention through non-porous floors and humidity control, while industrial settings focus on structural reinforcement for heavy multi-cylinder storage.
Safety Protocols and Handling Procedures
Both medical and industrial applications of nitrous oxide demand stringent safety protocols to prevent decomposition and control exposure risks. You’ll need to implement strict valve operation procedures, using slow-opening mechanisms and oxygen-compatible lubricants to prevent adiabatic compression. Clean all surfaces thoroughly before N₂O contact and maintain reduction valves free from contamination.
For exposure control, you must utilize gas detection systems and maintain proper ventilation. The gas requires proper storage conditions in cool, dry places to ensure stability and safety. Always wear personal protective equipment in medical settings and adhere to NIOSH’s 2 ppm ceiling for halogenated anesthetics. Your incident response procedures should include immediate evacuation protocols upon leak detection, verification with detection equipment before re-entry, and swift medical attention for exposure symptoms.
Keep emergency controls EPA-compliant and prioritize personnel safety during spills or decomposition events.
Quality Control Measures
Quality control measures for food and industrial grade nitrous oxide vary remarkably across five key domains: certification standards, raw material sourcing, purification processes, audit frequency, and contaminant management.
Food grade production demands rigorous batch consistency through ISO 22000/FSSC 22000 certifications and HACCP implementation, while industrial grade follows less stringent ISO 9001 protocols. You’ll find food grade facilities undergo frequent certification auditing by regulatory authorities, maintaining thorough documentation of quality control procedures.
Their multi-stage purification processes target human-safe purity levels, whereas industrial grade focuses on meeting technical specifications. Raw material sourcing for food grade prioritizes minimal impurities and prevents contamination through strict controls. Industrial grade allows cost-effective materials with acceptable impurity thresholds, using less intensive purification methods suited to technical applications rather than consumption safety.
Application-Specific Requirements
When working with nitrous oxide, you’ll find that medical applications require strict adherence to safety protocols, including specialized training for personnel and precise dosing equipment, while industrial uses follow more general OSHA guidelines. The FDA and USP govern medical-grade nitrous oxide with stringent regulations.
You’ll need to implement rigorous production control standards for medical-grade N2O, maintaining 99.9%+ purity through advanced filtration and testing processes. Industrial-grade tanks operate at a notably lower 98% purity level. The distinction in handling requirements becomes evident in the packaging and delivery systems, where medical applications demand tamper-evident seals and traceable supply chains, contrasting with industrial grade’s more flexible storage and distribution methods.
Safety Protocols and Handling
Safety protocols for nitrous oxide diverge markedly between medical and industrial applications, reflecting their distinct operational scales and risk profiles. You’ll need to implement specific equipment maintenance protocols based on your facility type, with medical settings requiring oxygen-compatible lubricants and self-contained recycling systems, while industrial facilities demand dry-run interlocks and adiabatic compression prevention.
Parameter | Medical Grade | Industrial Grade |
---|---|---|
TWA Exposure Limit | 25 ppm | 50 ppm |
Ventilation Rate | 10-15 air exchanges/hr | Based on hazard class |
Safety Systems | Automatic scavenging | Multiple interlocks |
Environmental Impact | Closed recycling | Direct ventilation |
Environmental impact considerations vary dramatically, with medical facilities prioritizing contained gas recovery through scavenging systems, while industrial settings focus on broader atmospheric monitoring and leak detection protocols.
Production Control Standards
Production control standards between medical and industrial nitrous oxide manufacturing reveal five distinct regulatory frameworks that drive their respective quality assurance processes. Medical-grade production adheres to stringent ISO 22000 and FSSC 22000 certifications, incorporating HACCP systems and comprehensive facility design requirements that guarantee food safety compliance.
Staff training protocols in medical facilities focus on pharmacopeia standards and FDA regulations, while industrial manufacturing follows ISO 9001 guidelines with less rigorous oversight. You’ll find medical production requires multi-stage purification processes and pharmaceutical-grade raw materials, maintaining strict limits on volatile organic compounds (<20 ppm).
In contrast, industrial grade accepts higher impurity thresholds, with technical-grade ammonium nitrate (82-93%) and elevated ammonia levels (<500 ppm). Quality testing frequency and depth also differ extensively, with medical production demanding more frequent third-party audits.
Documentation and Traceability Systems
The documentation and traceability systems for medical-grade and industrial-grade nitrous oxide reflect stark differences in their regulatory requirements and operational standards. Medical-grade systems implement all-encompassing cylinder serialization through RFID or barcode tracking, enabling precise monitoring in hospital settings with detailed batch numbers and expiration dates for individual containers.
Medical-grade documentation management requires full production stage traceability, including detailed lot records linking to raw materials and manufacturing processes. In contrast, industrial-grade systems utilize simpler documentation, employing generic lot numbers for bulk storage and manual logging for tank refills. While medical facilities must maintain patient exposure records and equipment maintenance logs, industrial applications focus primarily on basic inventory tracking without the stringent documentation requirements of their medical counterparts.
Frequently Asked Questions
Can Industrial Grade Nitrous Oxide Be Converted to Medical Grade?
You can’t convert industrial-grade nitrous oxide to medical-grade due to several technical barriers. The purification process would require extensive reprocessing to remove chemically bonded sulfur dioxide additives and meet pharmaceutical standards.
Storage conditions also pose a challenge, as industrial containers don’t meet medical-grade biocompatibility requirements. The conversion process would be costlier than producing new medical-grade gas, making it economically unfeasible.
What Happens if Medical Grade Nitrous Oxide Expires?
When your medical grade nitrous oxide expires, you’ll face several critical issues. Storage life degradation can lead to compromised gas purity and potential contamination from tank deterioration.
You’ll notice potency reduction, making the gas less effective for medical procedures. The expired gas may contain reduced oxygen levels and increased impurities, posing risks like hypoxia or neurotoxicity. You must dispose of expired tanks according to biohazard protocols to maintain safety standards.
Why Does Medical Grade Nitrous Oxide Cost More Than Industrial Grade?
You’ll find medical-grade nitrous oxide costs more due to its stringent production requirements. The higher purity levels (99.9%+) demand sophisticated filtration processes and specialized equipment.
You’re also paying for extensive quality testing, FDA-compliant documentation, and rigorous batch validation. Distribution logistics add further costs through specialized medical-grade cylinders, controlled transportation requirements, and strict chain-of-custody protocols to maintain pharmaceutical-grade standards.
How Often Should Nitrous Oxide Storage Tanks Be Inspected?
You’ll need to conduct regular tank inspections according to specific schedules: external visual checks during each filling cycle, annual ultrasonic thickness testing per STI SPP001 requirements, and internal inspections when external issues arise.
Proper tank maintenance includes safety relief device functionality tests and non-destructive testing protocols. You must maintain detailed documentation of all inspections in compliance with § 180.215 and OSHA standards, using certified personnel for all evaluations.
Are There Different Disposal Requirements for Medical Versus Industrial Nitrous Oxide?
You’ll need to follow distinct disposal protocols based on the grade. For medical N2O, you must implement proper disposal protocols that often require high-temperature incineration to eliminate potential contaminants.
Industrial N2O can typically be vented through exhaust scrubbers after monitoring tank pressures. Before disposal, you’ll need to verify complete tank emptying and follow local regulations for both grades to guarantee environmental compliance.